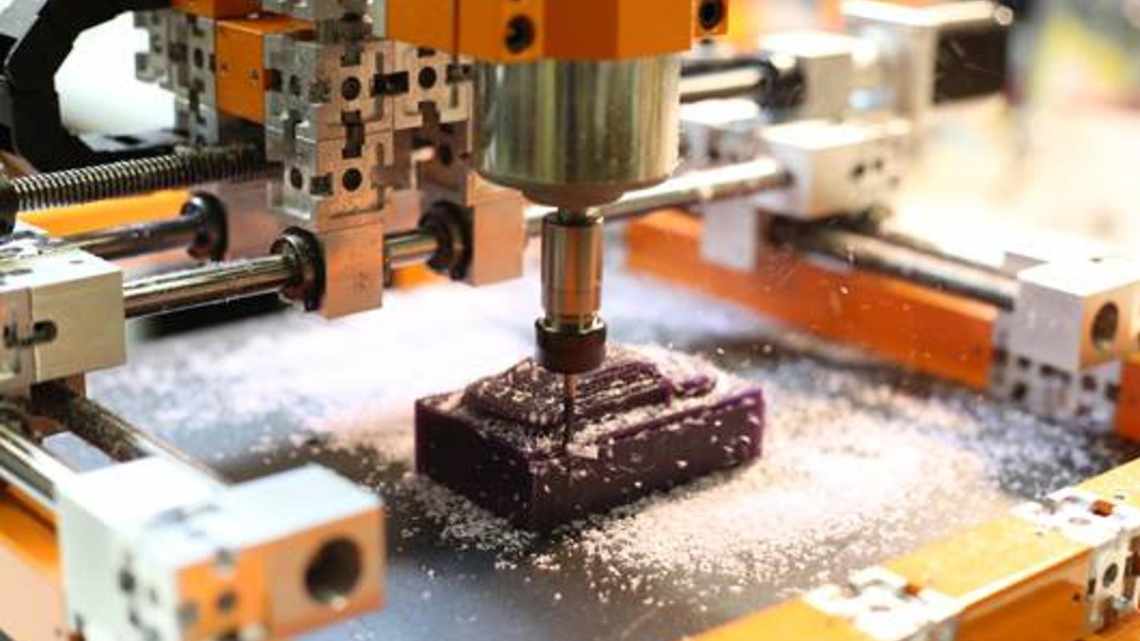
3D-друк збільшила міцність і пластичність сталі
Американські дослідники розробили метод 3D-друку виробів з аустенітної нержавіючої сталі, який дозволяє при тому ж складі сплаву отримувати більш міцні і пластичні вироби, ніж за допомогою звичайних методів. Стаття опублікована в журналі.
У промисловості застосовується безліч видів сталі, що розрізняються як за складом, так і за механічними властивостями. Частина з них має високу міцність, інші можуть сильно деформуватися без руйнування, але комбінація цих властивостей являє собою велику проблему для вчених. У той же час, багато вчених займаються розробкою таких сплавів через їх затребуваність.
В останні роки дослідники також займаються і іншою проблемою - застосуванням 3D-друку в металургії. Ця технологія дозволяє створювати конструкції такої форми, яка складно реалізована або зовсім недосяжна за допомогою звичайних методів виробництва. Наприклад, у 2016 році General Electric представила новий турбогвинтовий двигун, і за рахунок застосування 3D-друку змогла скоротити кількість деталей у ньому з 845 до 11. Проблема 3D-друку металами полягає в тому, що найчастіше при виробництві металевих виробів застосовується багатоступенева механічна і термічна обробка, через яку вони набувають потрібні властивості, але при друку провести таку обробку неможливо.
Дослідники навчилися друкувати нержавіючою сталлю, і одночасно збільшувати таким чином міцність і пластичність виробів порівняно з виробництвом іншими методами. Для цього вони використовували технологію лазерного спікання матеріалу в заздалегідь сформованому шарі (L-PBF). При такому методі друку лазерний промінь розплавляє порошок в потрібних місцях, переміщаючись по шару, після чого спеціальний апарат формує новий шар порошку поверх нього. Вчені вибрали цей метод через високу швидкість ствердування, що дозволяє отримувати нерівноважні структури.
Як матеріал дослідники використовували хромонікелеву аустенітну нержавіючу сталь 316L. Однією з проблем при друку такою сталлю є висока пористість, через яку вона стає малопрочною і схильною до тріщиноутворення. Вчені змогли за допомогою моделювання та експериментів знайти параметри лазера, при яких частка пір в кінцевому виробі становить менше 0,8 відсотка. За рахунок цього вони змогли отримати ієрархічну структуру з безліччю кордонів і дислокацій. Провівши серію механічних випробувань вони з'ясували, що така структура дозволила створити при однаковому складі більш міцні зразки, ніж отримані за допомогою лиття і ковки.
Нещодавно NASA розповіло про створення і випробування займальника рідинного ракетного двигуна, надрукованого на 3D-принтері з двох сплавів. Передбачається, що технологія друку двома сплавами дозволить використовувати набагато менше деталей і на третину скоротити витрати на виробництво двигунів.